Downtown “Funky Stuff” Malone🍆
Verified Military
Ladies & Gents,
I have always sent my AR barrels and gas blocks to a machinist to get the barrels dimpled for the gas block set screws. I also have them pinned as an extra layer of reliability.
I have been looking at a product for some time and finally decided to pull the trigger and start doing the process my self.
They are pinning jigs for YHM and VLTOR gas blocks and a universal dimppling jig by BRD Engineering.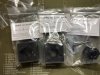
MOD EDIT. This is not an advertisement for sale or service. The intent is meant to be a point of information.
I have always sent my AR barrels and gas blocks to a machinist to get the barrels dimpled for the gas block set screws. I also have them pinned as an extra layer of reliability.
I have been looking at a product for some time and finally decided to pull the trigger and start doing the process my self.
They are pinning jigs for YHM and VLTOR gas blocks and a universal dimppling jig by BRD Engineering.
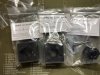
MOD EDIT. This is not an advertisement for sale or service. The intent is meant to be a point of information.
Last edited: